Many industrial applications rely on pressure transducers to efficiently and safely operate and maintain equipment. If a pressure sensor fails, it can cause the entire control system to fail and lead to inoperable equipment or system down time; depending on the type of system, significant damage can occur to the equipment and surrounding environment. For systems experiencing periodic pressure spikes, damage due to a failed pressure sensor can often be prevented if the sensor selection processes considers overpressure resilience.
Why do sensors fail?
Pressure transducers can fail for a variety of reasons. One of the most common causes of failure is overpressure. Most standard industrial transducers are either strain gauge or piezoresistive sensing based and are not built to withstand overpressure, especially in lower pressure operating ranges. Strain gauge based sensors typically have limited overpressure ratings of 3X FS. Piezoresistive MEMS sensors are often even lower with only 2X FS proof pressure ratings.
Avoiding overpressure damage with a standard pressure sensor tends to mean selecting a higher pressure range than desired. This can severely impact accuracy and usable analog outputs. An example of this is selecting a 5,000 PSIG range to resist overpressure damage instead of the needed 100 PSIG to monitor water pressure.
What is overpressure?
Overpressure is the maximum pressure a transducer can endure without an impact on performance. Transducers experience overpressure when the pressure value exceeds this limit. Pressure transducers can tolerate occasional pressure spikes up to their overpressure rating; although this is not ideal, the transducer eventually returns to its normal state. Causes of overpressure include fluid hammer, unintentional heat applied to the system, water freezing, and a faulty pressure regulator.
Burst pressure can permanently damage a transducer. Burst pressure is the maximum pressure that can be applied to the positive pressure port without physically damaging the internal sensing component. Experiencing burst pressure can rupture the transducer's diaphragm and cause leakage. When a transducer undergoes pressure above the overpressure rating but below burst pressure, its diaphragm becomes permanently deformed, leading to an output shift impacting operational performance and accuracy readings.
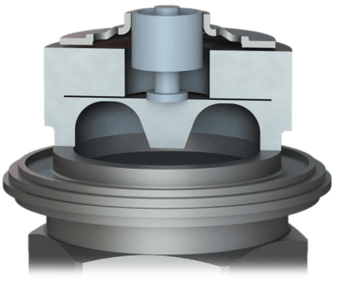
Resisting Overpressure Damage
The most effective way to combat the potential damage from overpressure is to choose a sensor with a high overpressure option. Setra's Model AXD industrial pressure transducer is built to withstand the harsh conditions of industrial applications or unexpected pressure bursts. With an option for high overpressure protection up to 10X FS, the AXD is a robust capacitance transducer. Setra's patented overpressure stop prevents the sensor from bursting while allowing the diaphragm to maintain its shape.